Apprentice produces the right notes
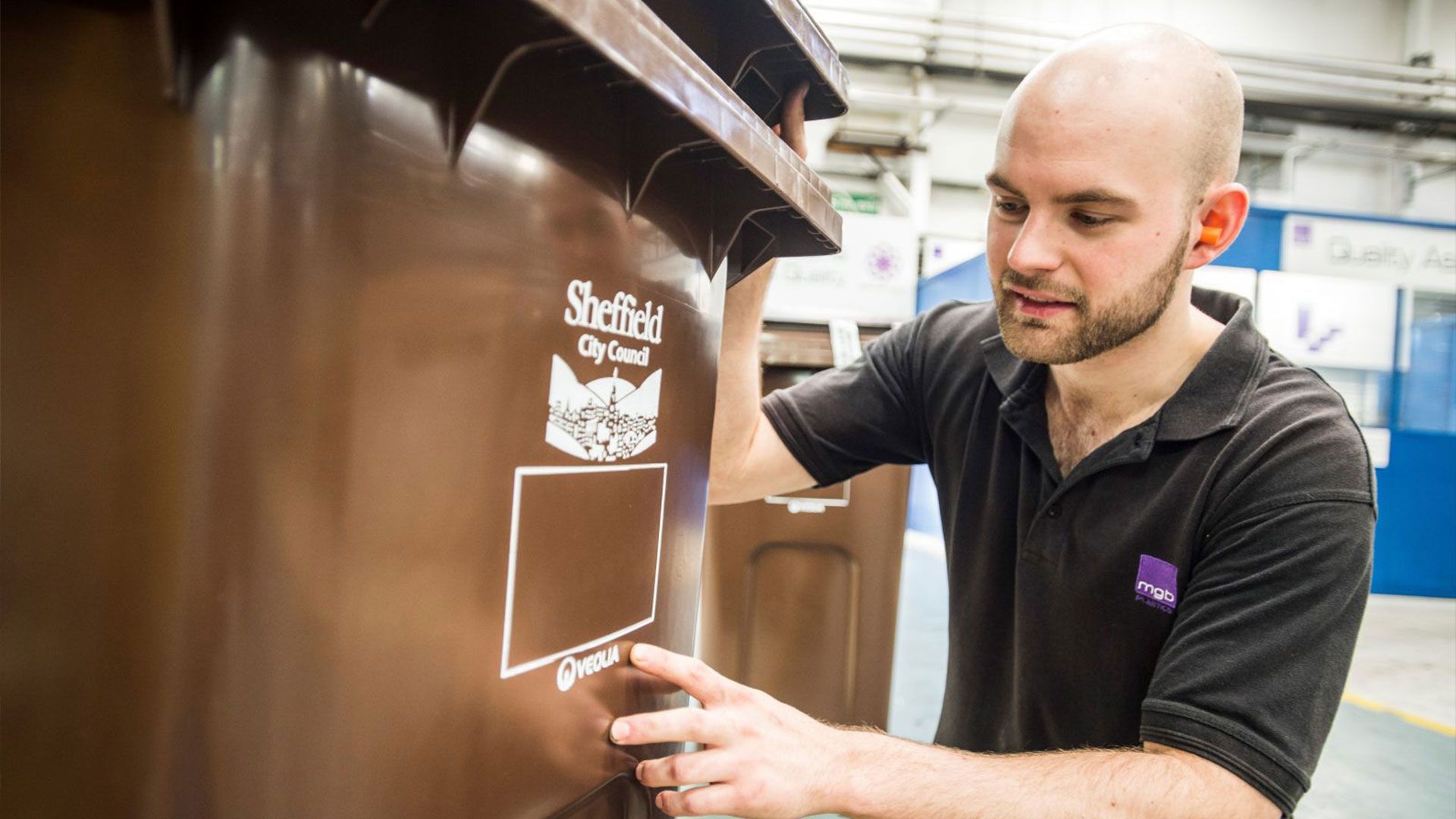
University of Sheffield AMRC Training Centre apprentice, Oliver Marsh, has scooped a major industry apprenticeship award for his role in helping the UK’s largest manufacturer of wheelie bins reduce the cost of its production processes by more than £135,000 a year.
The 21-year old aspiring rock musician, an apprentice with the OnePlastics Group, was the clear winner in the plastic industry’s equivalent of the Oscars – Polymer Apprentice of the Year Award, the official ceremony for which will be held in London next month.
Barnsley-born Oliver, who works in the state-of-the-art, highly automated MGB Plastics factory in Rotherham, said he was delighted to win the award: “It’s a privilege and an honour to get this award. Working at MGB has been brilliant; the company has given so much support and encouragement. My mentors at work have taught me how to use lean techniques and processes to drive improvements in productivity and performance.”
Having recently invested more than £25 million in advanced technology, including large presses, the company was equally keen to invest in its human capital: training the next generation of polymer engineers who will maximise the impact of this investment in its three plants at Rotherham, Tamworth and Hull.
MGB Plastics Technical Manager, Gary Blanshard, said the company wanted to bring bright young engineers into the business to enable it to maintain its position as the market leader in the supply of wheeled bins. “We decided that the best way forward was to get someone on board who had no pre-conceived ideas of how things should be done. The only way to do this was to train them from scratch,” Gary said.
“We invited the AMRC Training Centre to visit us and discuss what they could offer in the way of apprenticeships. They then advertised for a Technical Apprentice and created a short list of candidates. After an extensive interviewing, Oliver was offered the position and began his apprenticeship with us.
“Having gained knowledge of CAD at the AMRC Training Centre, he has used this to great effect with us. He used CAD to model the fit of our lids, which some customers had identified as an issue, and found a mismatch between the hinge fixing pin and the bin mating hole. He redesigned the pin and improved the tolerances using CAD. Having tested a prototype and run moulding trails on the new hinge pin, he proved out the fit and function through assembly trials.”
But it is Oliver’s work in improving the moulding process that has most impressed the company. By using the lean principles taught to him by his close mentors at the plant. “He has transformed what was already a market leading printing technology used to emboss the more than 1.5 million bins we produce each year,” said Blanshard. “His forensic examination of the change-over process from one council crest to another has turned the operation into the polymer equivalent of a Formula One pit stop – fast, efficient and very slick.
“We estimate that this improvement alone is saving the business in excess of £137,000 a year by getting the plate changes down to just 34 seconds from 10 minutes. It is a brilliant example of a single-minute exchange of die (SMED) approach, which Oliver has picked up very quickly and developed with us.”
Oliver is now a key member of our plant automation team tasked with taking significant costs out of the business, and is looking at how the firm’s existing equipment might need to be uplifted to meet new standards for the industry. “If there is a productivity-critical issue, Oliver is in the mix,” said Gary.
A keen musician, Oliver is the bass player in the band Alba Rosa – White Rose – who recently supported The Lost Days at the 02 Academy. Oliver is now in the enviable position of a being centre stage in both his new engineering role, and driving bass lines with the band.