Patrick Bentley
Published on 25/02/2025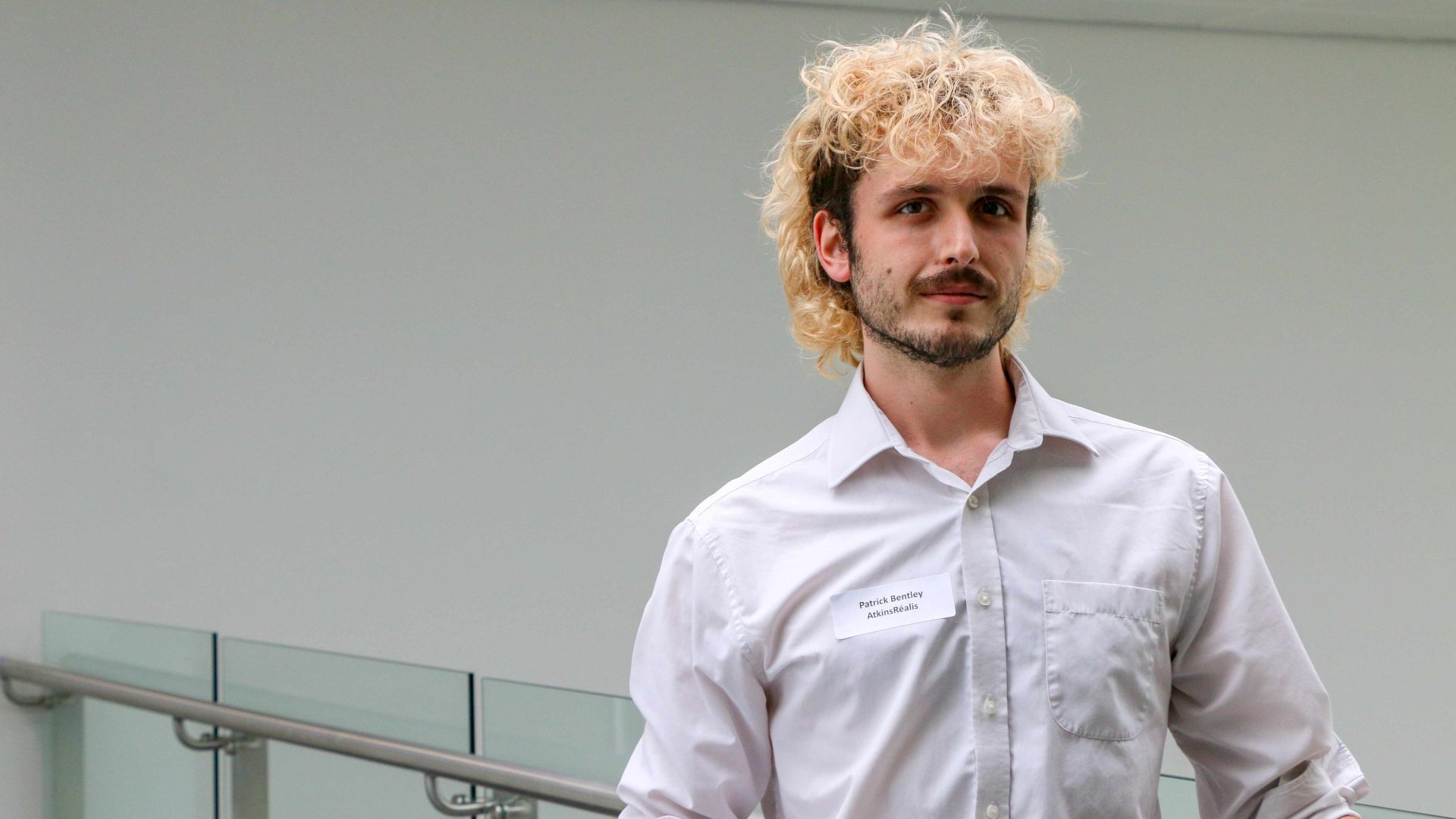
Name: Patrick Bentley, 21
Job title: Mechanical engineer
Employer: AtkinsRéalis
Studying: Mechanical manufacture degree apprenticeship
Pathway: product design and development engineer
Q. What inspired you to pursue a career in engineering?
I think it was a combination of multiple factors. I have always been good at maths and physics, which is often what attracts people to engineering. Besides, my dad is an engineer too, so seeing what he does for work was pretty cool.
I also found it interesting to watch people build things on YouTube. Plus, I’ve always enjoyed building things myself and understanding how they work. So basically, my job now is exactly what I love to do
Q. Why did an apprenticeship appeal to you?
I’m a very hands-on learner, so I prefer learning on the job. I like to be challenged, and an apprenticeship seemed like the perfect fit. Obviously, there’s classroom learning, but it’s also a job. So it seemed like a great way to jump straight into the engineering world without having to do a degree first.
My year was also a bit of a gamble. A-levels of the year before me were cancelled due to COVID-19, and with my A-level being cancelled too, it was tough to get into university. A lot of people deferred their applications, making competition fierce. Plus, the thought of going to university for the experience but being locked down in a dorm room instead didn’t appeal to me. I wasn’t going to pay for that.
An apprenticeship offered a perfect lower-risk option, and I was already excited to start working as an engineer.
Q. How do you think your apprenticeship will give you the skills and knowledge you need for a rewarding career?
It’s tough to pinpoint specific academic skills I’ve used at work. While I haven’t applied mechanics or stress analysis directly, my general math skills have been invaluable. Understanding equations, relationships, and how changes affect outcomes is crucial for engineering tasks. For example, I can predict the impact of increasing a bolt diameter on stress.
Beyond technical skills, soft skills like presentation abilities have been an equally important lesson that I have learned. Being able to communicate effectively is really useful in any engineering role.
Q. What was the best part about doing an apprenticeship at the AMRC Training Centre?
The way my degree apprenticeship was designed specifically for apprentices, unlike some ad hoc apprenticeship programs through universities that focus more on academic theory. Our course was practical, focusing on the skills I’d need in the industry. For example, our thermodynamics professor taught us about internal flows in pipework, which is more relevant to real-world engineering than external flows.
Although my course was more traditional mechanical engineering, I’m aware that other AMRC Training Centre programs like manufacturing technology focus on Industry 4.0 and emerging technologies like generative artificial intelligence – making those courses look ahead to the future of engineering which is a great curriculum.
Q. What tips and/or advice would you give to other people looking to do an apprenticeship?
It’s tough, and it’s okay to admit that. Many people put unnecessary pressure on themselves to do well, but it’s important to acknowledge the demanding nature of the course. It’s hard work and a lot of balance. There’s a lot of stuff going on at the same time and while balancing everything can be challenging, time management is really important.
Burnout is a real risk, so keeping track of your own mental health and making sure you're taking breaks is essential. And it’s okay to struggle. Even if people around you seem to have it easy, everyone faces difficulties. It’s normal.
Q. Tell us about your final project.
My project focused on investigating potential impacts of mass imbalance in SpinChem rotating bed reactors (RBRs), which are used to deploy ion exchange resin to clean liquid nuclear waste. RBRs are essentially rotating tanks that use centrifugal force to push liquid through resin beads, removing undesirable elements (including radionuclides) from the liquid, depending on the resin deployed.
One of the considerations to be made is the potential for mass imbalance to contribute to instability in a fault scenario. If this was severe enough, it could lead to increased stress on the shaft, potentially reducing its lifespan.
To investigate this issue, I developed six load cases based on different mass imbalances and analysed their effects they would have on the shaft. I found that while quadrant imbalances can contribute to vibration, they’re likely not the primary cause of the observed deflection.
I believe that shaft imperfections and resonance could be more significant factors. To mitigate these potential shortfalls, I investigated damping the system with polyurethane bumpers and using a secondary bearing to reduce shaft length. These modifications could significantly reduce stress and extend the lifespan of the RBR.
I also postulated two potential fault cases: drying imbalances and quadrant leaks. These could lead to extreme mass imbalances and potentially break the shaft, posing a significant radiological hazard if they were to occur based on my assumptions and calculations.
Q. How can your project work impact the wider industry?
My project has improved the feasibility of a product called Spinionic, developed in collaboration between AtkinsRéalis and SpinChem to bring Spinionic to the nuclear industry. RBRs allow for in-situ deployment of ion exchange and are versatile such that they can also be used for upstream or post processing around other effluent management systems. It’s an in-situ solution for cleaning liquid nuclear waste. Unlike traditional ion exchange columns, which require extensive pipework and safety measures, Spinionic can be simply lowered into a tank or pond.
The work I have done, while purely theoretical, will likely form the basis of future discussions and analysis work in the future regarding mass imbalance and deflection.
Inspired to start your apprenticeship journey?