Moving to CNC
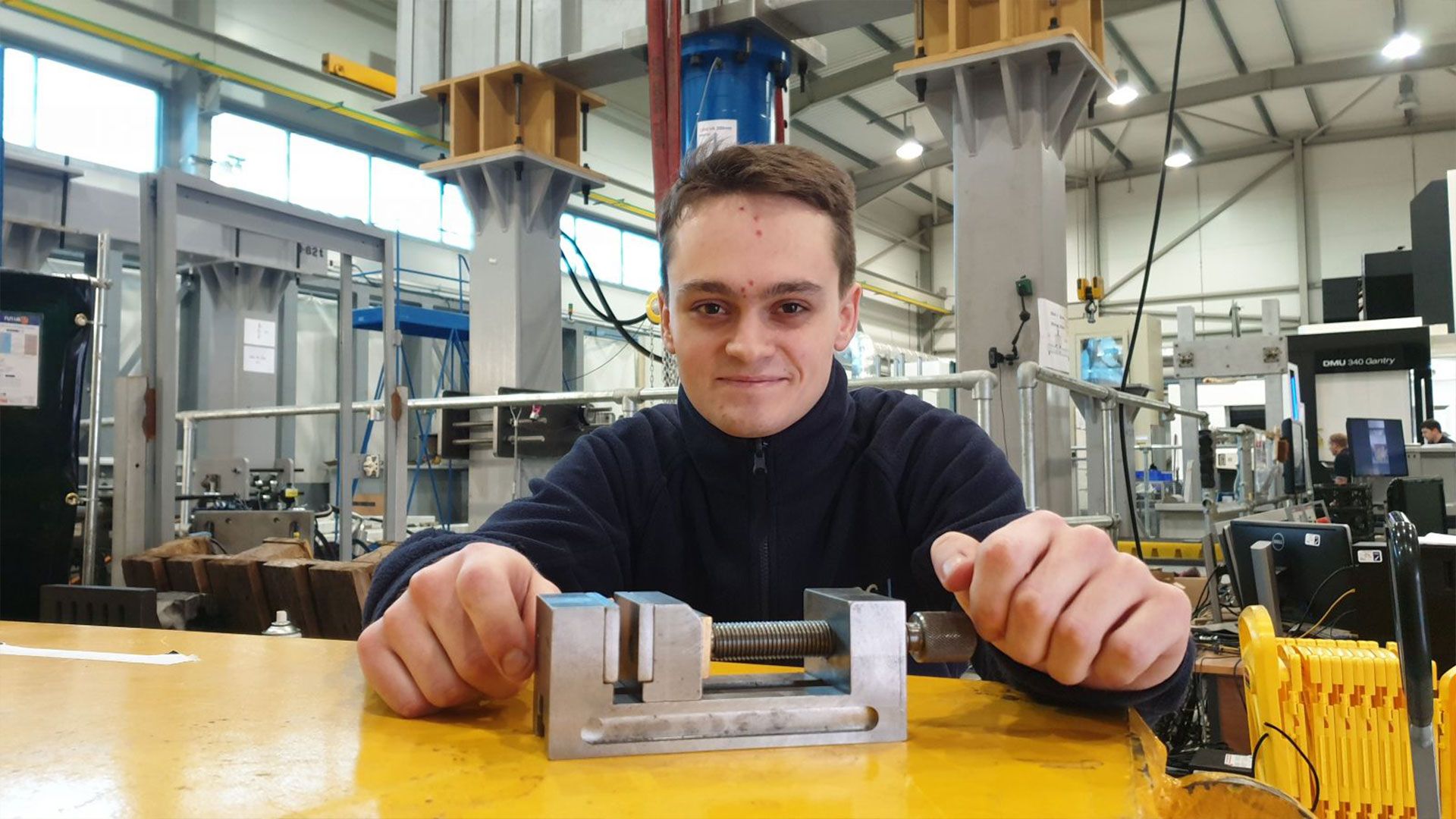
Jaw plates and jib strips
Jan 10, 2020
This past week I completed my vice. I had to produce two jaw plates, the jib strip and retaining plate as well returning to the main vice body to bring the ends down to size and produce the various threaded holes. To do this I had to fit an angle plate to the bed of the machine and clock it with a DTI (dial test indictor) to set it square to the machine. I then deburred and polished all the pieces. It was a great relief when all the pieces fitted together after some filling and re-running dies and taps through the more difficult pieces, but I was very happy when it all finally came together. I then helped some others who were still finishing, particularly with clocking the angle plate square. I am currently working on the paperwork to sign off on the project, which is a necessary part of learning to be an effective machinist. I am looking forward to moving onto the CNC machines next week as I have never used one before and it will be a totally new experience.
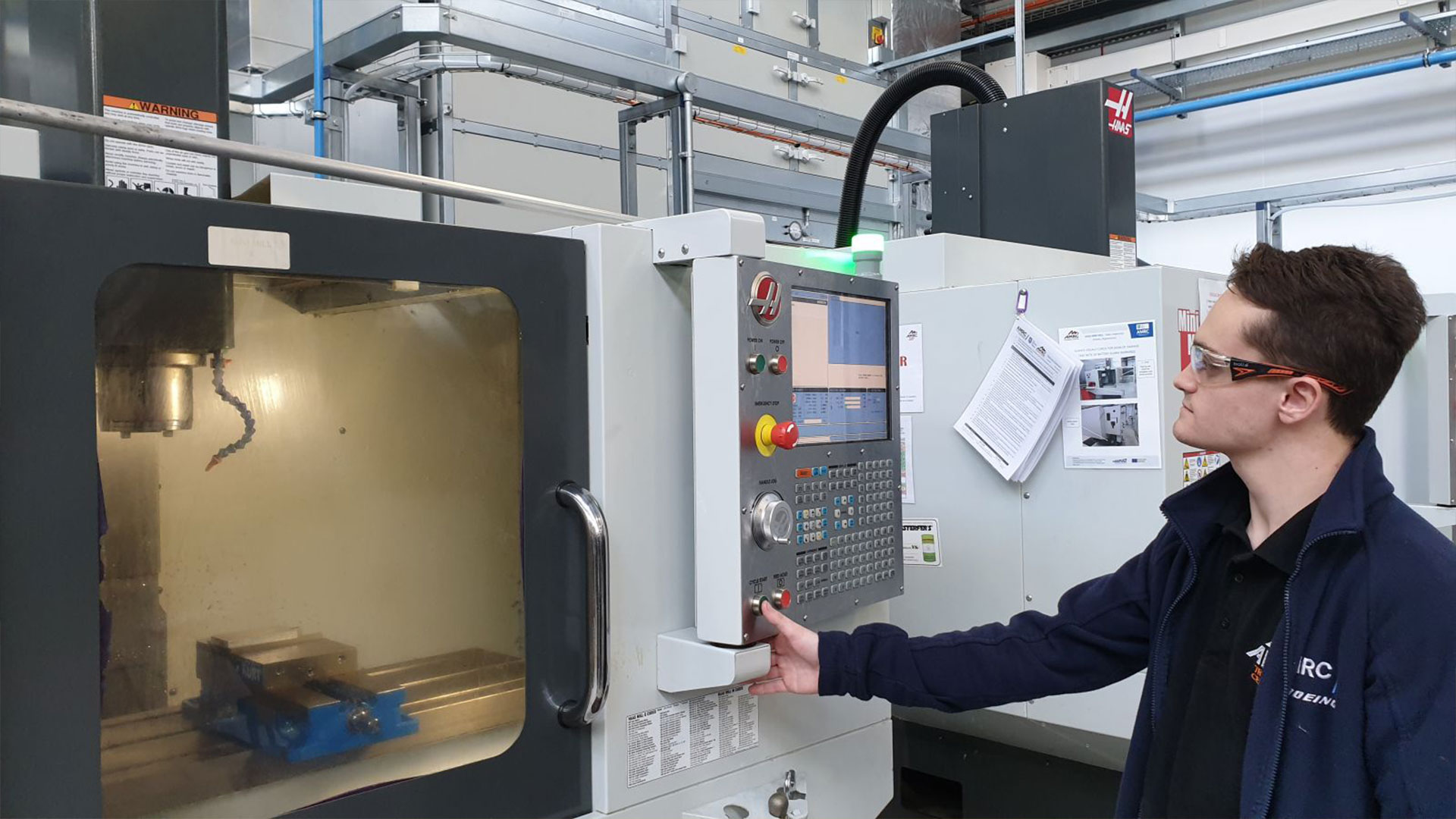
Moving from manual to CNC milling
Jan 17, 2020
I have finished the paperwork for my vice and therefore completed manual milling. I am very happy with how the past seven weeks went as I now feel comfortable and able to undertake manual milling in the work place to a good standard. On Monday we moved onto CNC milling where I will spend the next seven weeks. The machines we will be using are manufactured by HAAS but until then we will be practising on simulators which have an identical control panel to the machines. We began on the machine by programming some simple codes like having the spindle move in the X and Y plane in the shape of a square with radii and chamfers on the corners. It was much easier than I had expected as all the information on the monitors at first seemed quite overwhelming but it took only a few hours before I could program some simple functions.
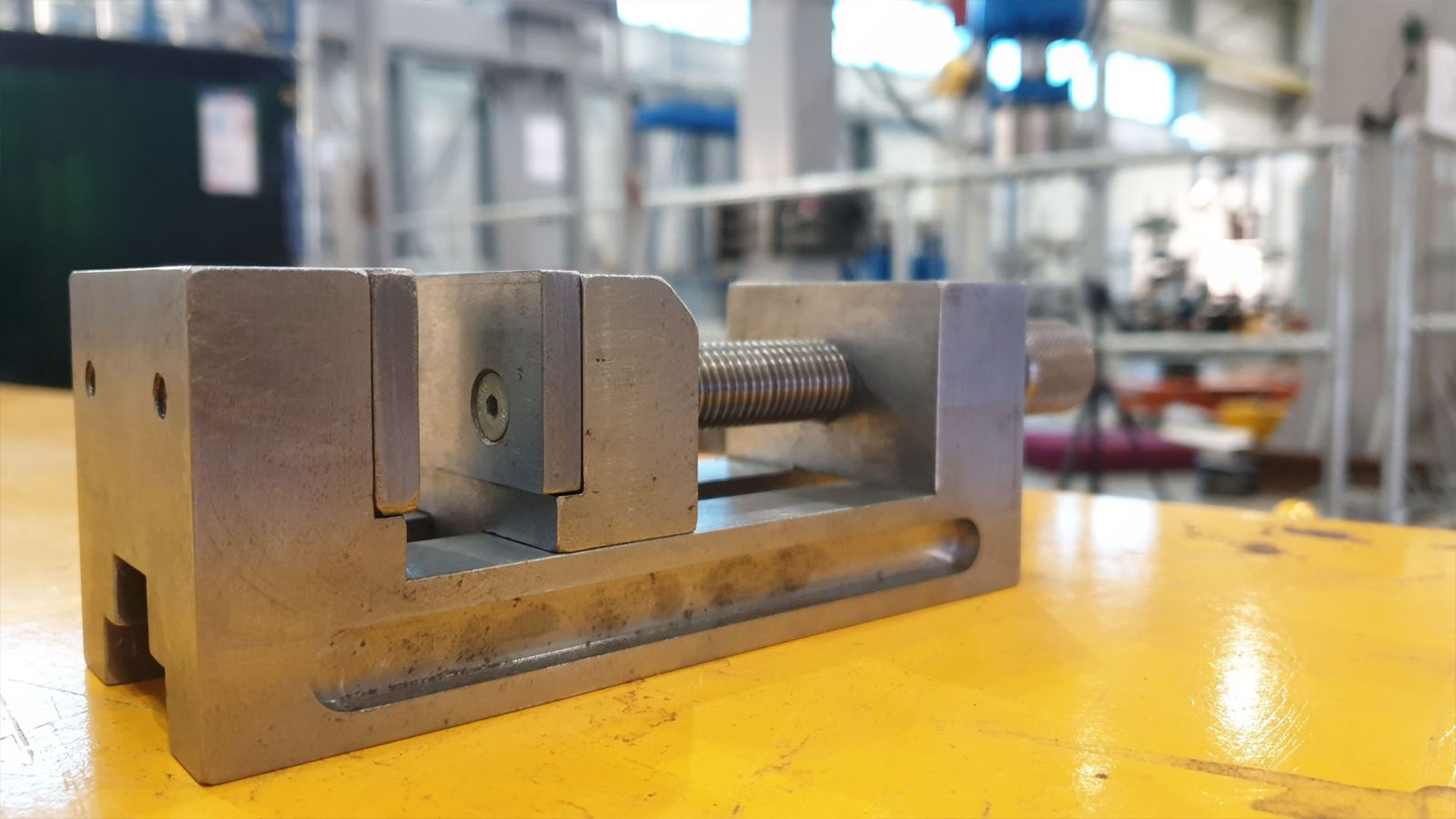
Going above and beyond
Jan 24, 2020
On ‘return to work Friday’ the AMRC ASTC team were kind enough to allow me to continue my professional development as I saw fit. So I decided that I would continue to make improvements to my vice beyond what was required in the assessment. I decided to drill a hole through the knurled handle to accommodate a steel tommy bar. I then began to make various jib strips from different materials, such as brass and PTFE so that I could decide which material best suited for each application. I very much enjoyed doing this because it made the vice feel more like my own creation because I had gone further and made my own alterations and improvements rather than just following someone else’s drawing.
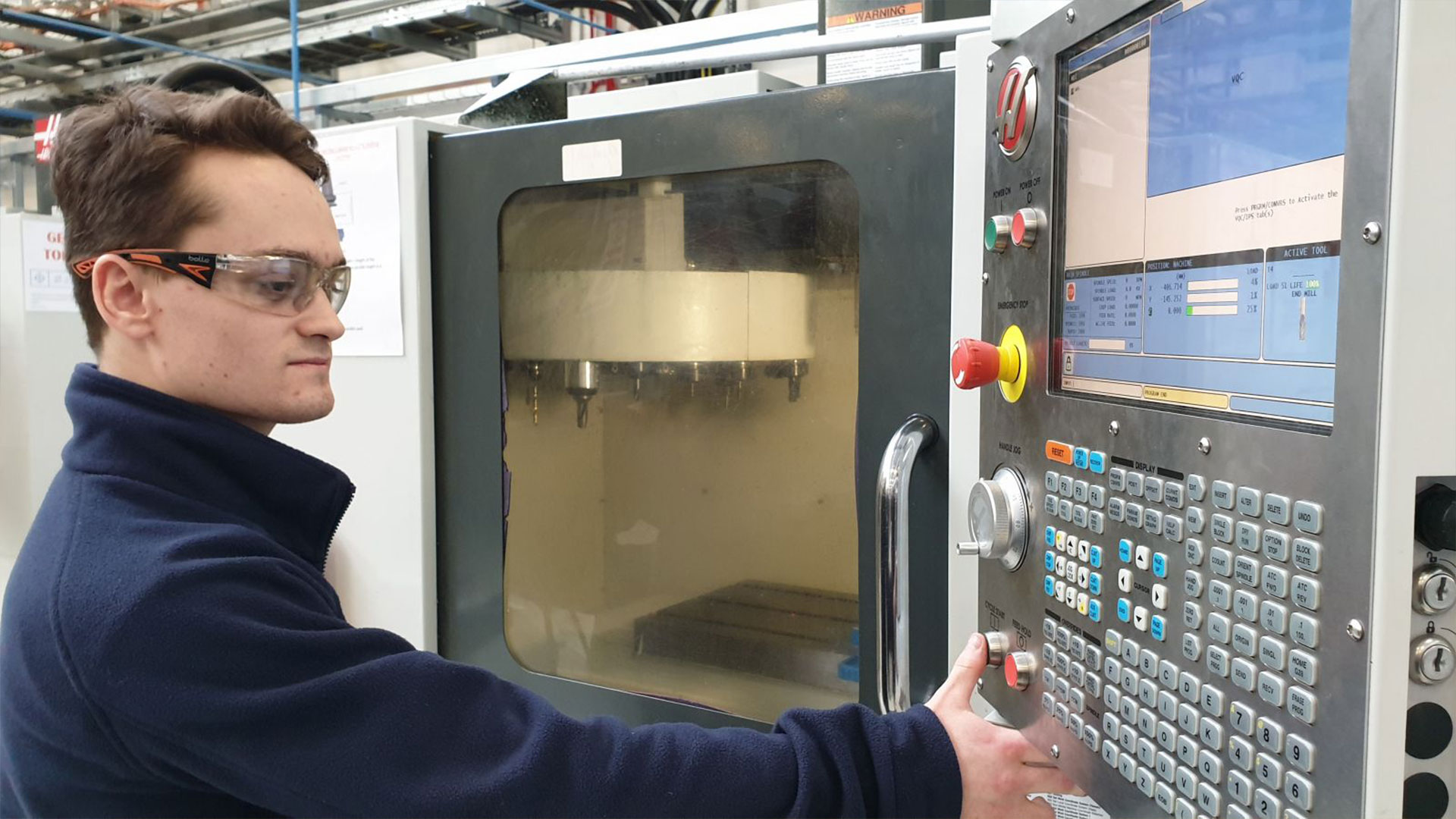
Setting the CNC
Jan 31, 2020
This week I have been learning how to manually set the CNC milling machine and run a pre-designed program. This was surprisingly similar to the manual milling. I expected the machine to have an internal detection system that could set the machine to the workpiece. But instead, many of the functions were similar to manual milling, such as finding the zero with the wobble bar and setting the vice square with a DTI (Dial Test Indicator). Another interesting change was how the machine could hold all the required tools and how you had to set the tools in accordance with the program. It was quite tense when I set the machine running for the first time since, but luckily I completed the piece without breaking any tools.