Ian Pengkerego
Published on 21/01/2025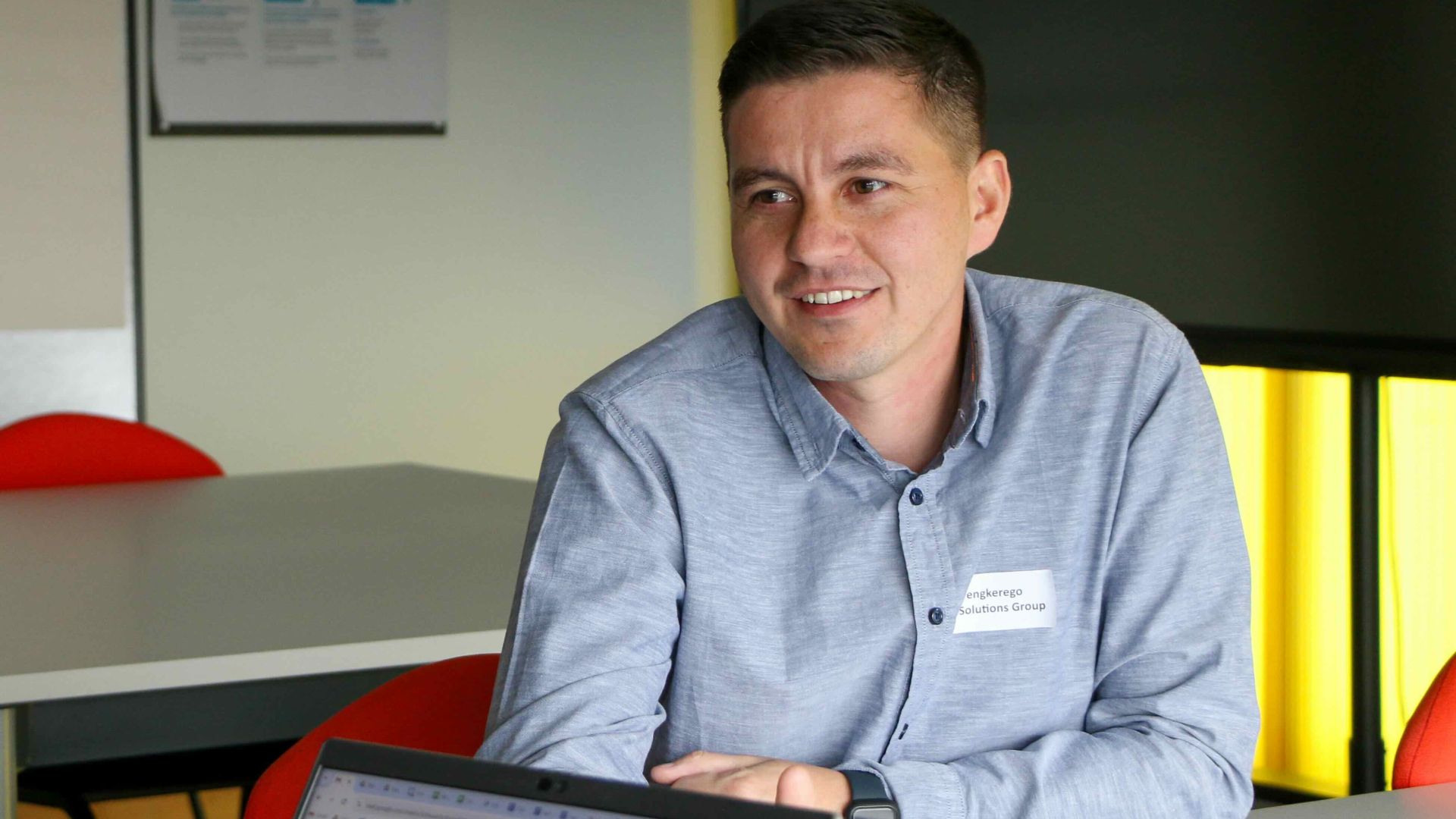
Name: Ian Pengkerego, 36
Job title: Lead manufacturing engineer
Employer: Forged Solutions Group
Studying: Mechanical manufacturing degree apprenticeship
Q. What inspired you to pursue a career in engineering?
I've always had a passion for engineering, especially the steel industry, which has a deep-rooted history in Sheffield. Growing up here, I was inspired by the idea of contributing to this heritage. Although I didn't have the chance to study engineering in school, I pursued it after graduation, starting with a level 3 apprenticeship. Over the next decade, I gained valuable experience in the industry before returning to formal education.
Q. Why did an apprenticeship appeal to you?
When I first left school at 17, I did a level 3 apprenticeship, which was a machine and engineering course. Initially, I considered pursuing A-levels but realised it wasn’t the right choice for me. Instead, I opted for an apprenticeship, which I believed was better suited with my career aspirations and what I wanted to do.
I've been working for the same company since my first job, where I've had the opportunity to explore various aspects of engineering. My current role at Forged Solutions has allowed me to see the entire manufacturing process, from hot works and forging raw material input right through to finished products. This constant learning has kept me engaged throughout my career.
After 15 years of industry experience, I enrolled for my current level 6 apprenticeship at the AMRC Training Centre. I have a demanding role within the company I work for, so it was impractical for me to quit my job and pursue full-time studies again. However, this apprenticeship provided me with a unique, flexible path to earn a degree and advance my skills while continuing to work. This new challenge, which I began at the age of 33, has helped me deepen my understanding of engineering principles.
Q. How do you think your apprenticeship will give you the skills and knowledge you need for a rewarding career?
My current apprenticeship has introduced me to new skills that complement my existing knowledge. These skills and the knowledge I've gained have directly supported my current role, which has evolved over the past three years. The recent changes in my role align more closely with the subjects I'm studying, allowing me to apply the skills and knowledge I've gained to my work at Forged Solutions.
I've leveraged these skills to contribute to the company's success. I've led several projects related to capital investment, and I'm proud to say that these projects have been very successful. And the skills I've developed through the apprenticeship have played an important role in my achievements.
Q. What was the best part about doing an apprenticeship at the AMRC Training Centre?
I’m returning to a learning environment after many years, so adjusting to exams, structure and an academic setting has been quite challenging. However, one of the most rewarding aspects has been meeting new people.
Interacting with the other 30–40 apprentices has been a valuable experience. I've learned a lot from them, especially the younger ones. In turn, I believe my industry experience has allowed me to offer them guidance and mentorship.
The advanced equipment available at the AMRC Training Centre is another plus. You don’t usually get exposed to technology like this in other industries. Additionally, the lecturers at the training centre are highly skilled and knowledgeable in their respective subject matters. Many of the senior lecturers have practical industry experience, and I have learned a lot from them.
Q. What tips and/or advice would you give to other people looking to do an apprenticeship?
Do it, that’s what I will say to anyone who asks. While I acknowledge that at times an apprenticeship can be difficult, and balancing a degree, work as well as personal life is demanding, I believe the rewards are worth the effort.
My personal circumstances are certainly different to many others – I’m older, married and have children to look after. So doing a degree while juggling it all has been quite challenging sometimes. But I’ve put in the work, and I’m receiving the reward.
I haven't always been the top student, but I've always worked very hard and that has allowed me to keep pace with my peers. And I’m hopeful that my efforts will also result in a first-class degree.
So my only advice to anyone who is doing or starting an apprenticeship soon is to just work hard and make the most of this opportunity.
Q. Tell us a little about your final project.
As a steel manufacturer primarily serving the aerospace industry, my project focuses on implementing operational excellence within our business. This involves adopting lean manufacturing techniques, inspired by the Toyota production system, to improve operational efficiency, productivity and overall business performance.
Coming out of the COVID-19 pandemic, the aerospace industry faced significant challenges. Our business struggled to maintain pre-pandemic levels because of disruptions in raw material supply and process inefficiencies. Due to uncertainties around the industry, many people left the industry that led to loss of skills.
My project aims to introduce improvement technologies to support our growth and return to pre-pandemic levels. And we've made significant progress in achieving this goal.
To implement operational excellence, we formed a large project team and introduced operating practices, such as daily production reviews. These reviews involve senior management engaging with shop floor workers to collaborate, identify problems and find solutions. It bridges the gap between the people who are doing the work, and the people that are leading the business who have an influence on fixing problems first hand.
Additionally, we've invested in equipment upgrades and implemented standardised practices, including 5S and planned preventive maintenance. These initiatives have significantly improved equipment reliability, reducing breakdowns and increasing production efficiency.
Q. How can your project work impact the wider industry?
One of the main benefits of implementing planned preventive maintenance was that it enabled us to move equipment availability from mid 70 per cent to 98 per cent in just six months. So we’ve now got more reliable equipment. This has positively impacted our business as Forged Solutions – we've met our business goals, increased efficiency and reduced energy consumption.
Moreover, our improved performance has also had a positive impact on the broader aerospace industry. We supply to major engine manufacturers, such as Rolls-Royce, Boeing and Safran. If we fail to supply a product, they can’t build engines. So our reliability is essential to their operations and is impacting engine build rates globally. By enhancing our own performance, we've contributed to the overall health of the aerospace supply chain.
Inspired to start your apprenticeship journey?