Wouter Swinnock
Published on 25/02/2025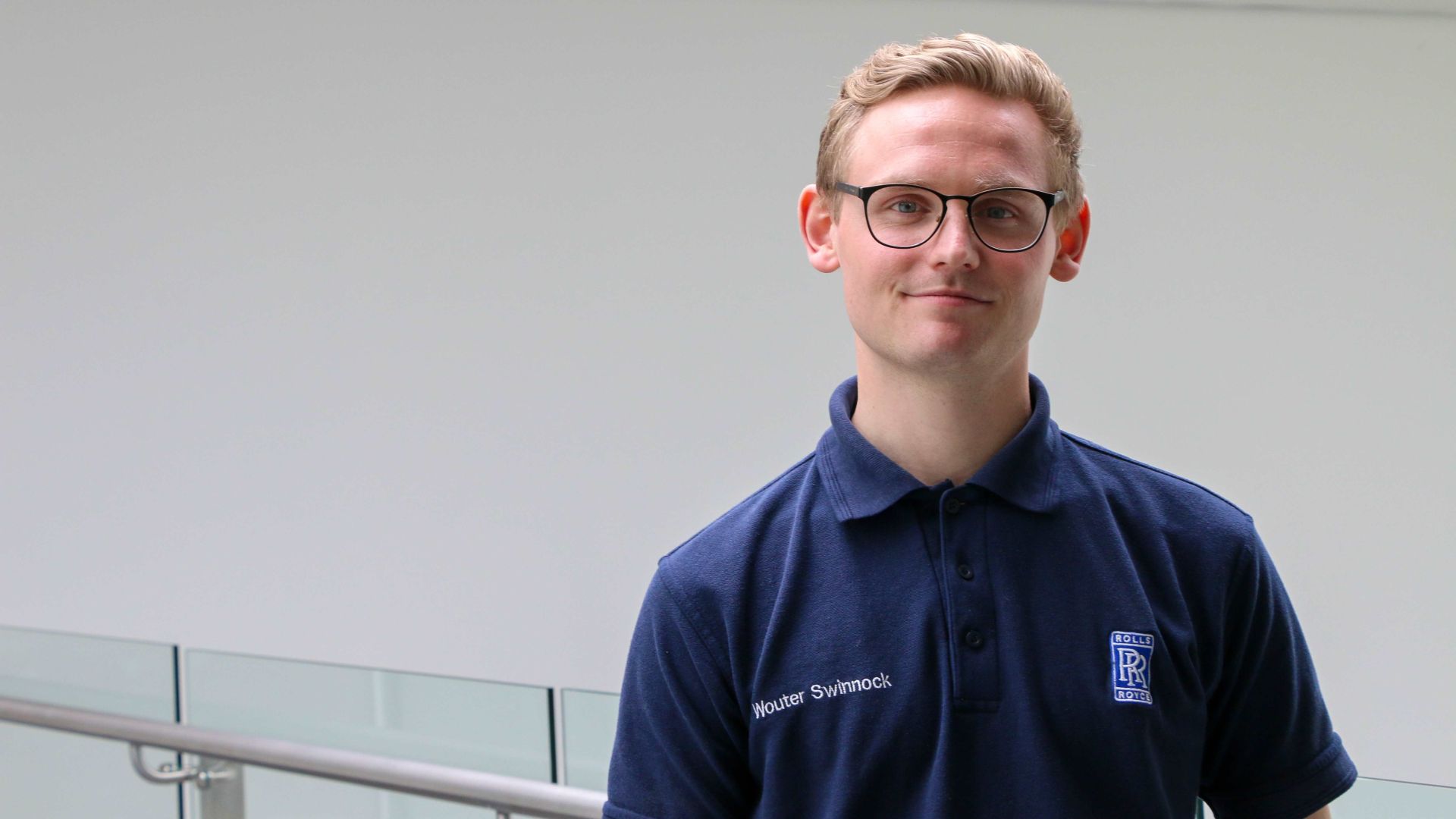
Name: Wouter Swinnock
Job title: Manufacturing engineering degree apprentice
Employer: Rolls-Royce
Studying: Manufacturing technology degree apprenticeship
Q.Who inspired you to pursue a career in engineering?
Growing up, I've always been passionate about sports, especially cycling and sailing. These activities require a mechanical mindset to understand pulley systems in sailing and gear systems in cycling. By fixing and tinkering with these things myself, I developed a strong mechanical aptitude.
While I was drawn to both engineering and business, I decided to pursue engineering as a foundation for business in the future. I felt that studying business first without a strong engineering background would limit my knowledge and capabilities.
Q. Why did an apprenticeship appeal to you?
At the time, I was really torn between choosing an apprenticeship and university, so I applied to both. I applied to numerous apprenticeship schemes and universities, while attending a university technical college called JCP Academy instead of a traditional sixth form. The academy was focused on industry and encouraged apprenticeships, which was a unique approach compared to the conventional push for university.
Many of my university friends regret not considering apprenticeships, since the route wasn’t fully advertised to them as a valid, available option. Apprenticeships offer financial benefits like earning a salary and avoiding student debt. This allows me to gain valuable work experience while potentially being four years ahead of traditional university graduates. If I decide the employer isn't a good fit, I can still pursue further education or find another job.
Q. How do you think your apprenticeship will give you the skills and knowledge you need for a rewarding career?
I believe the experiences I've gained with my employer are invaluable and will stay with me. In contrast, much of what I would’ve learned in university would’ve faded over time. While a degree is essential for entering the engineering field, practical experience is equally important. Being able to say, "I saved x million on a project at Rolls Royce," speaks volumes more than just listing degrees.
My job has also forced me to develop strong interpersonal and presentation skills. I regularly present my projects to senior colleagues and must justify their value, even if they don't immediately yield tangible benefits. I believe this rigorous questioning process pushes me to be the best version of myself.
Q. What was the best part about doing an apprenticeship at the AMRC Training Centre?
One of the best parts of doing an apprenticeship is the people you meet. You're surrounded by students from various companies, not just university students. I’ve made lifelong friends from different places, like Portakabin and other companies, which I wouldn't have found at a different training centre.
Q. What tips and/or advice would you give to other people looking to do an apprenticeship?
Talk to people who've already been through the program to get a realistic idea of what to expect. When I started, I wasn't sure which training provider I'd be going to. Talking to others helped me understand the potential challenges and what people have actually empirically seen, instead of relying solely on the information pushed by the program.
Don't be afraid to challenge things. If you think something isn't being done well, even at a prestigious company like Rolls Royce, because you think they must know what they’re doing – speak up. Chances are they might not have noticed what you have. Your insights can be valuable and help improve the program. So, don’t hesitate to suggest change.
Q. Tell us about your final project.
My project focused on the industrialisation of component transfers at Rolls Royce. We manufacture high-tech, sensitive components for jet engines in-house, but we outsource tasks involving lower technology in order to free up resources for innovation. However, I discovered that outsourcing often leads to engineering delays and increased costs due to validation issues.
I conducted a personal component transfer and interviewed 17 employees, from base level staff to vice presidents, to understand the challenges and impacts of these transfers. My research revealed systemic issues across different product types. I then published a company document outlining these issues and recommending considerations before undertaking future transfers .
For my research, I carried out a product transfer on a crucial engine component. This component travels through multiple manufacturing processes, including casting in Bristol, machining in Spain and Lincoln, and assembly in Loughborough and Derby. This complex supply chain highlights the excessive mileage and time involved before the component even reaches the engine.
I also discovered even more complex supply chains involving parts being shipped to and from China multiple times. This illustrates the potential negative impacts of such transfers on costs and timelines.
Q. How can your project work impact the wider industry?
My project can benefit the wider industry by providing confidence in component transfer decisions. Many companies have cost-saving ideas but hesitate to implement them due to the risk of delays and increased costs. My work demonstrates the importance of careful consideration and analysis to ensure that transfers are financially viable and executed efficiently.
At Rolls Royce, we have a backlog of potential cost-saving initiatives, often referred to as a "hopper." These ideas could save millions of pounds, but implementing them carries significant risks. We're uncertain about the actual return on investment, and delays could lead to even higher costs.
My work aims to address this hesitation by providing greater confidence in component transfers. With more confidence, companies will be more likely to implement these cost-saving ideas. This approach can be applied across various industries where companies often have promising ideas but are reluctant to implement them due to the fear of failure and incurring higher costs than expected. Ultimately, I think, instilling confidence is key to driving innovation and everything will follow.
Inspired to start your apprenticeship journey?